As part of the Aether project, I designed and digitally sculpted the motor cover in the rear of the car. This element is a safety feature, to prevent accidental contact with the high-voltage wires, but it was also an opportunity to create a more coherent design language across the entire car.
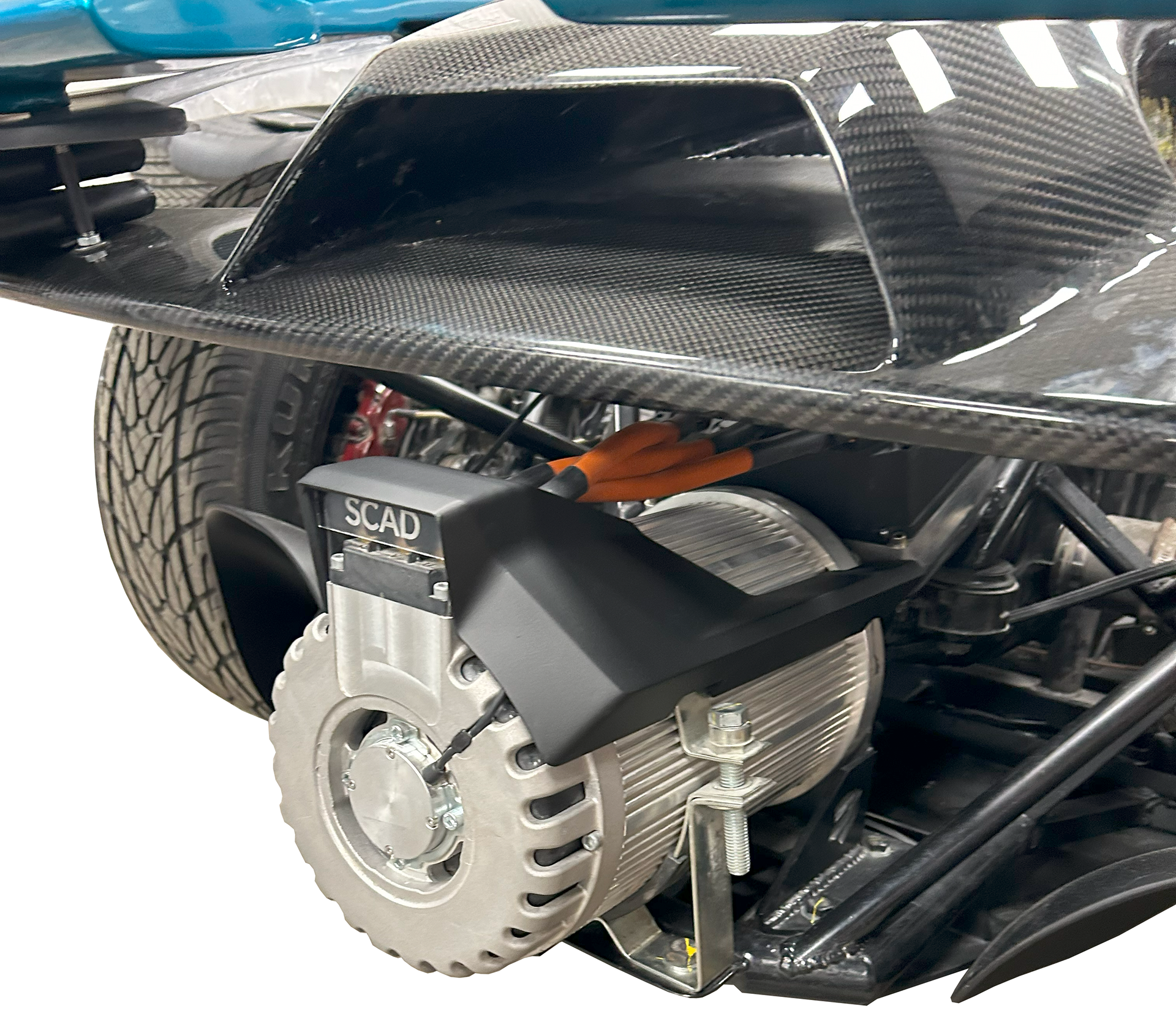
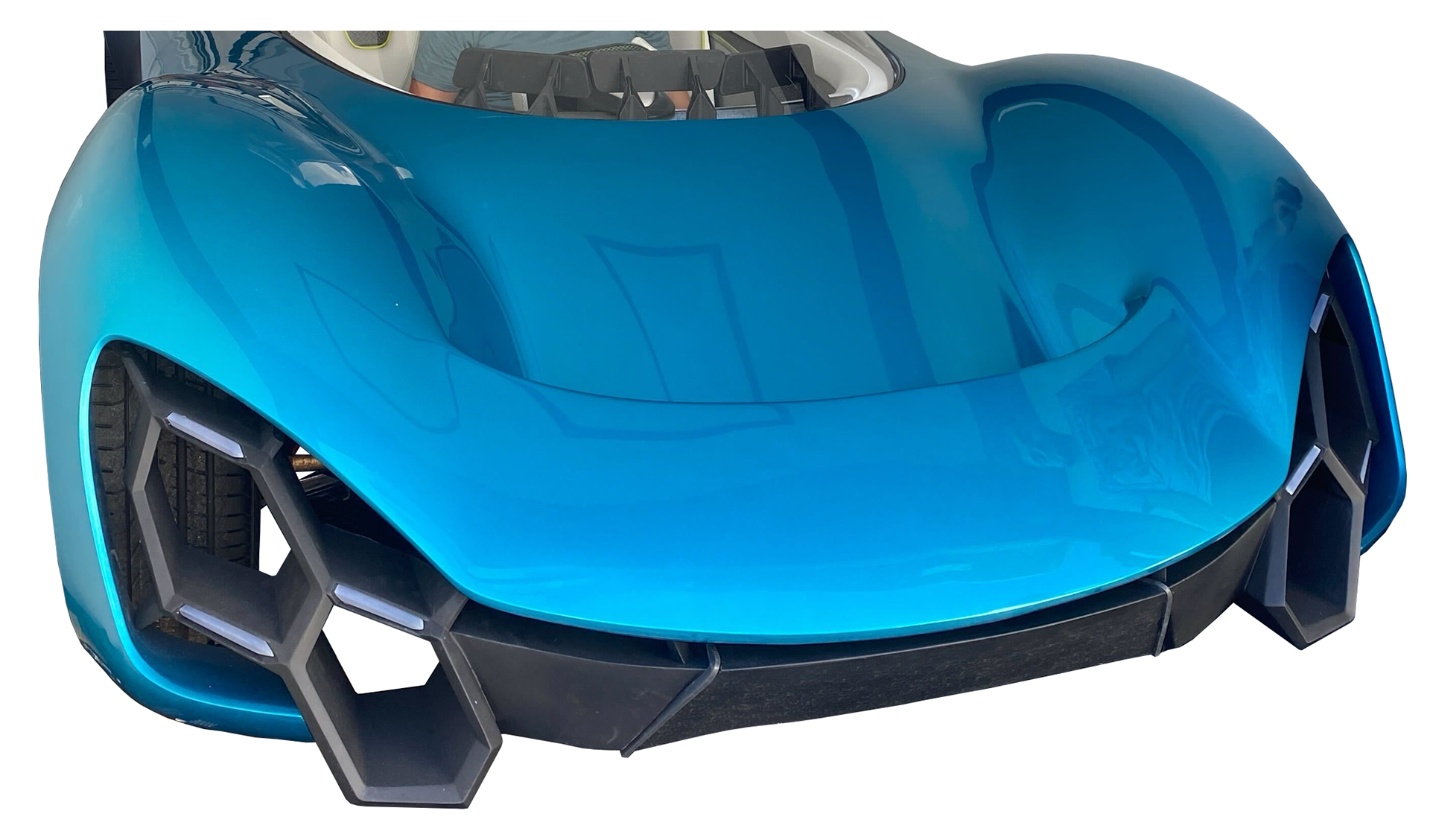
The motor cover design was intended to speak the language of the headlight housing. The front end, like the rear, is as open as can be. The huge ducts are like showroom windows for the wheels and suspension components. But the headlights, in addition to being a design element, serve as a protective barrier to the raw mechanics. Because this is also the criteria of the motor cover, a thematic link between them is natural.
Taking this concept to CAD (Rhino3D) was a new kind of challenge for me. When I did my first iteration of this model, I still had rudimentary skills in the program. I had no concept of the kind of work that goes into perfecting a surface. But I got some advice, read some forum posts, and bit by bit, the model improved. Pictured are the first, fifth, tenth, and final (sixteenth) iterations of the model.
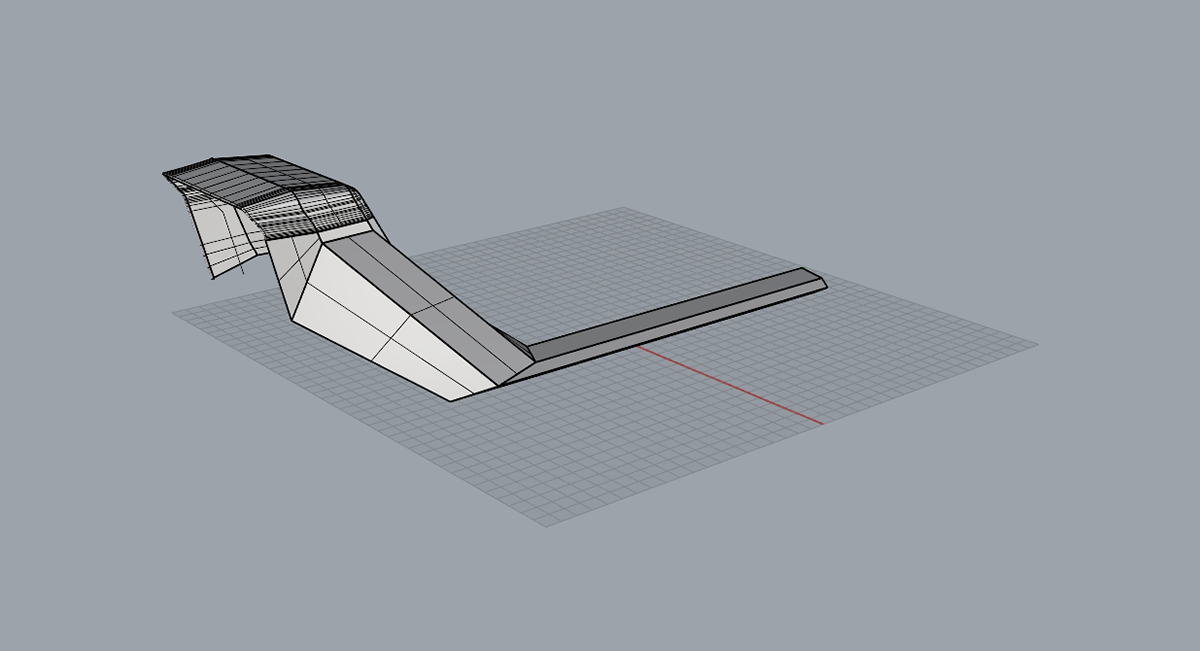
V1
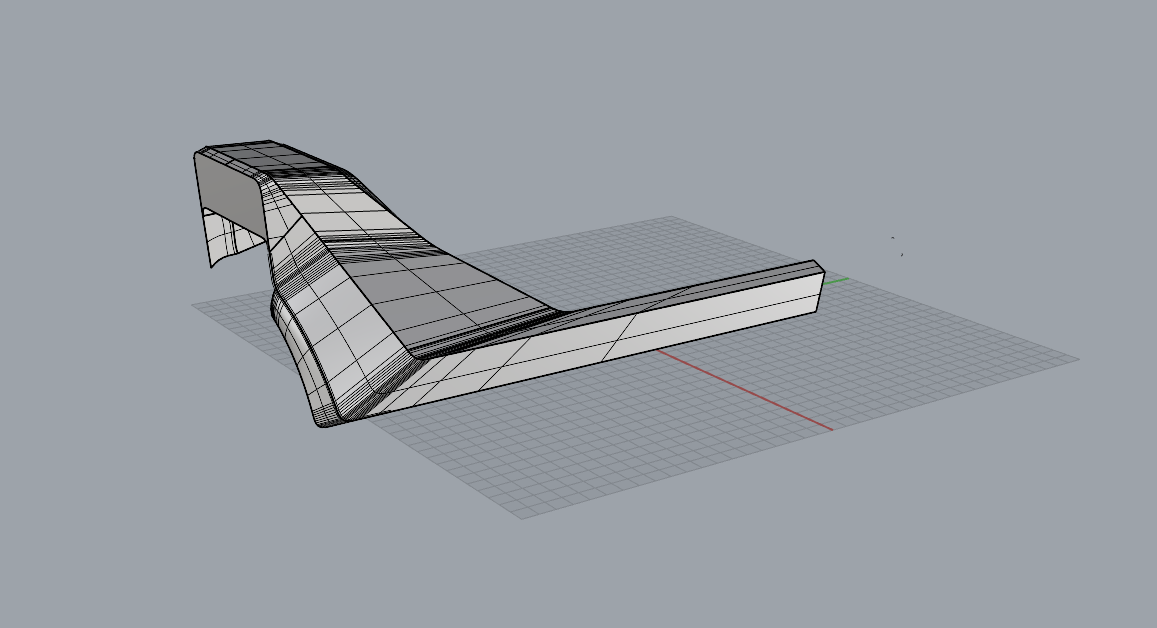
V5
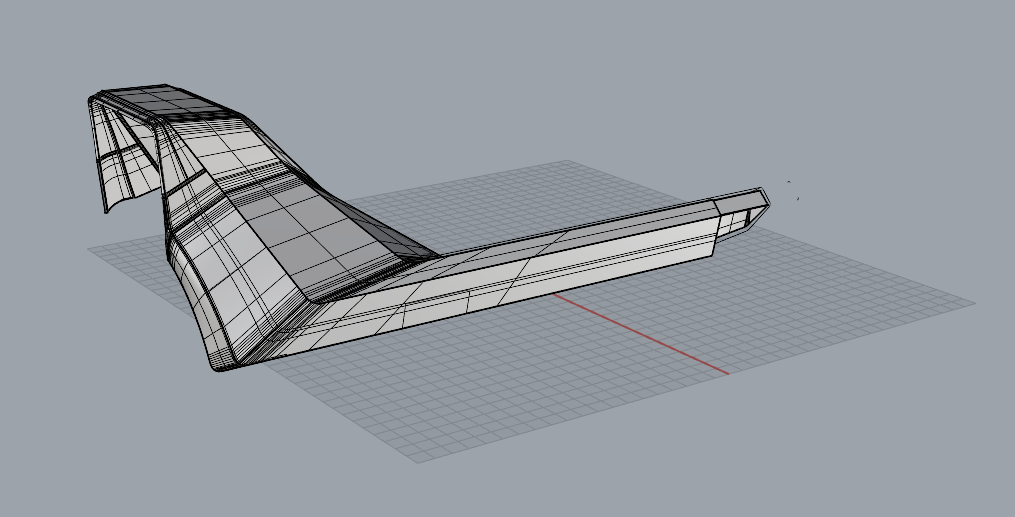
V10
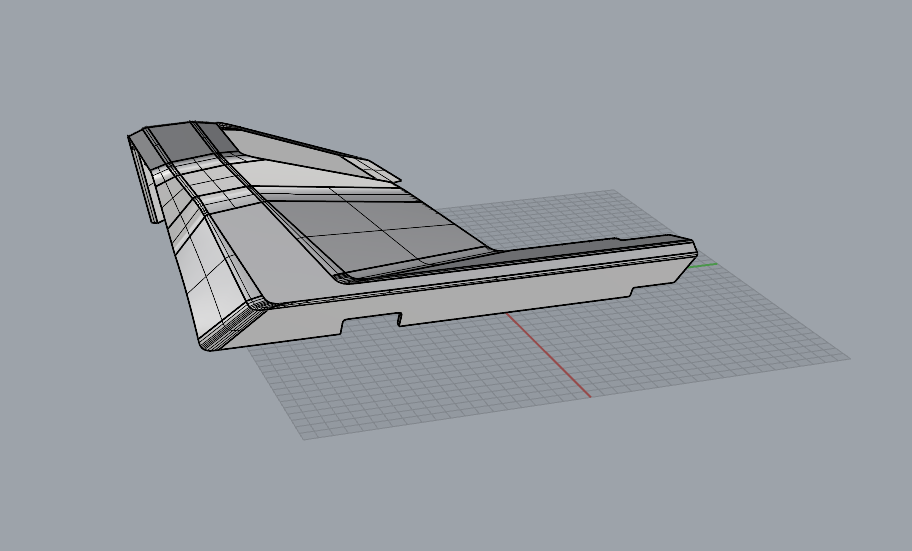
V16
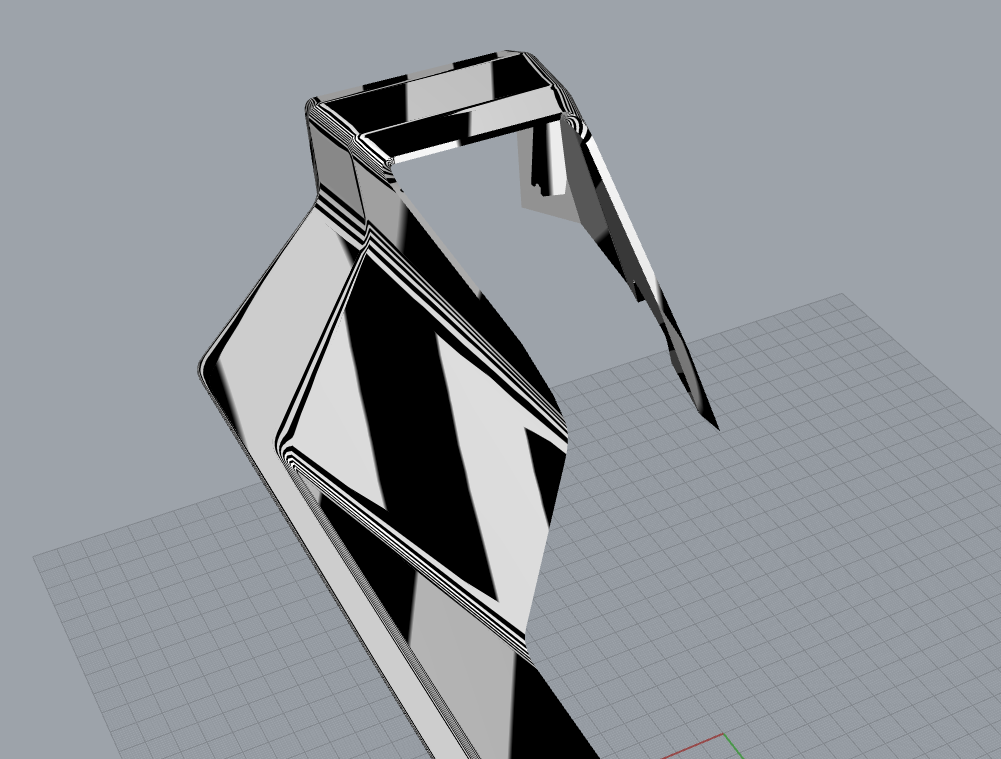
V16

V16
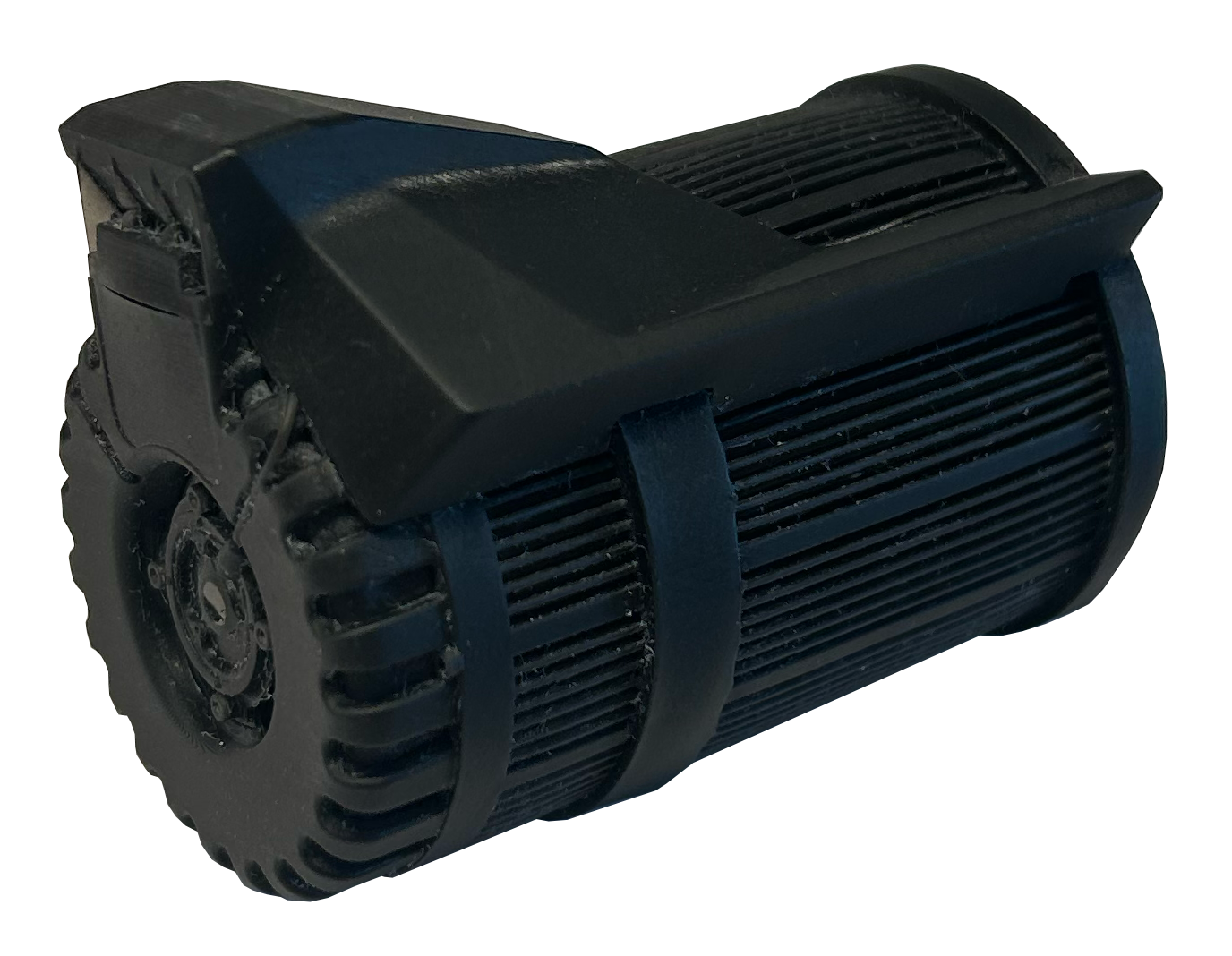
A resin-printed mockup of the cover with the motor at quarter scale.
The final model fresh off the 3D printer. Like most things on the car, it needed a bit of sanding, filler, and paint to get it show-ready.
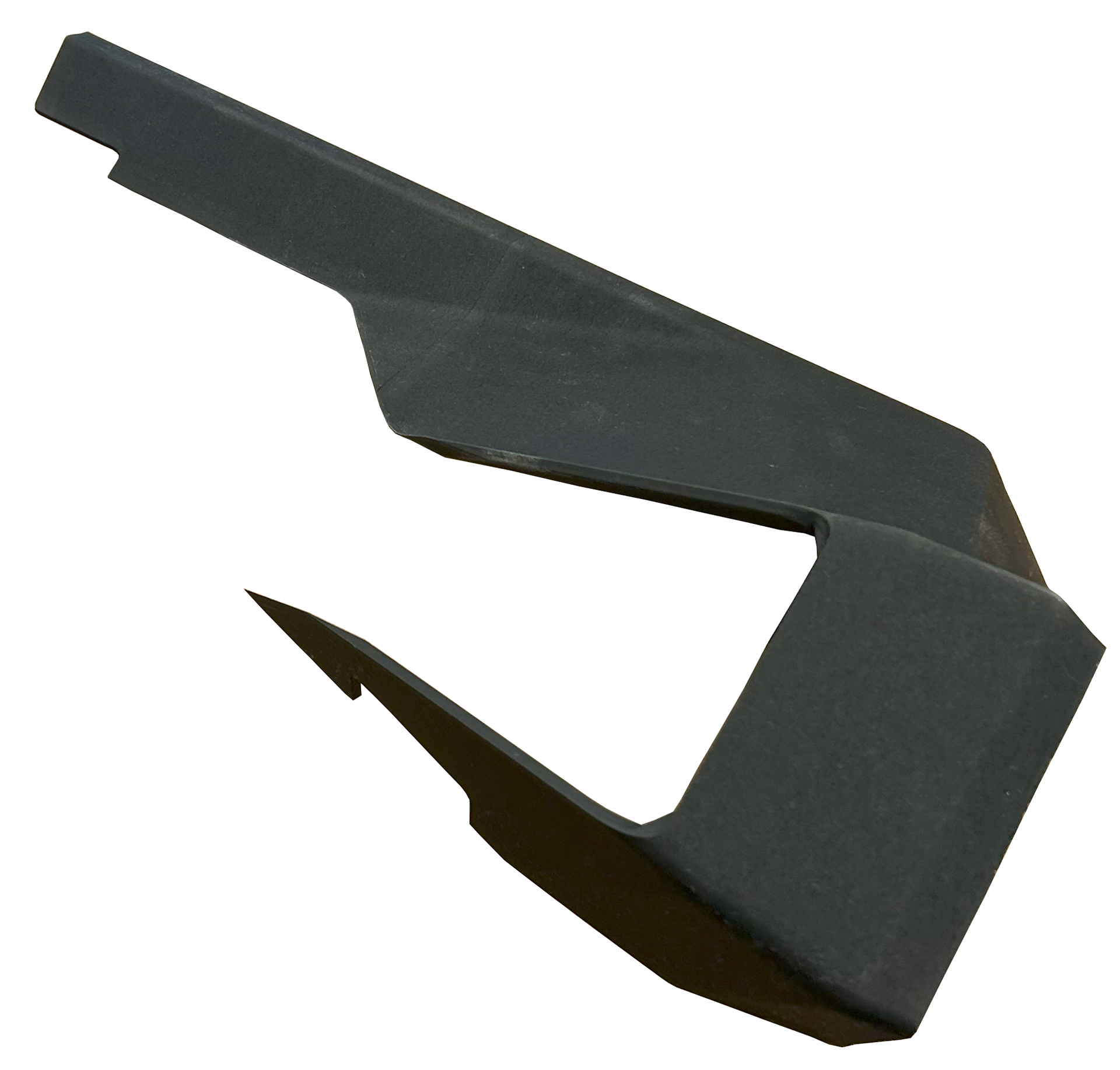