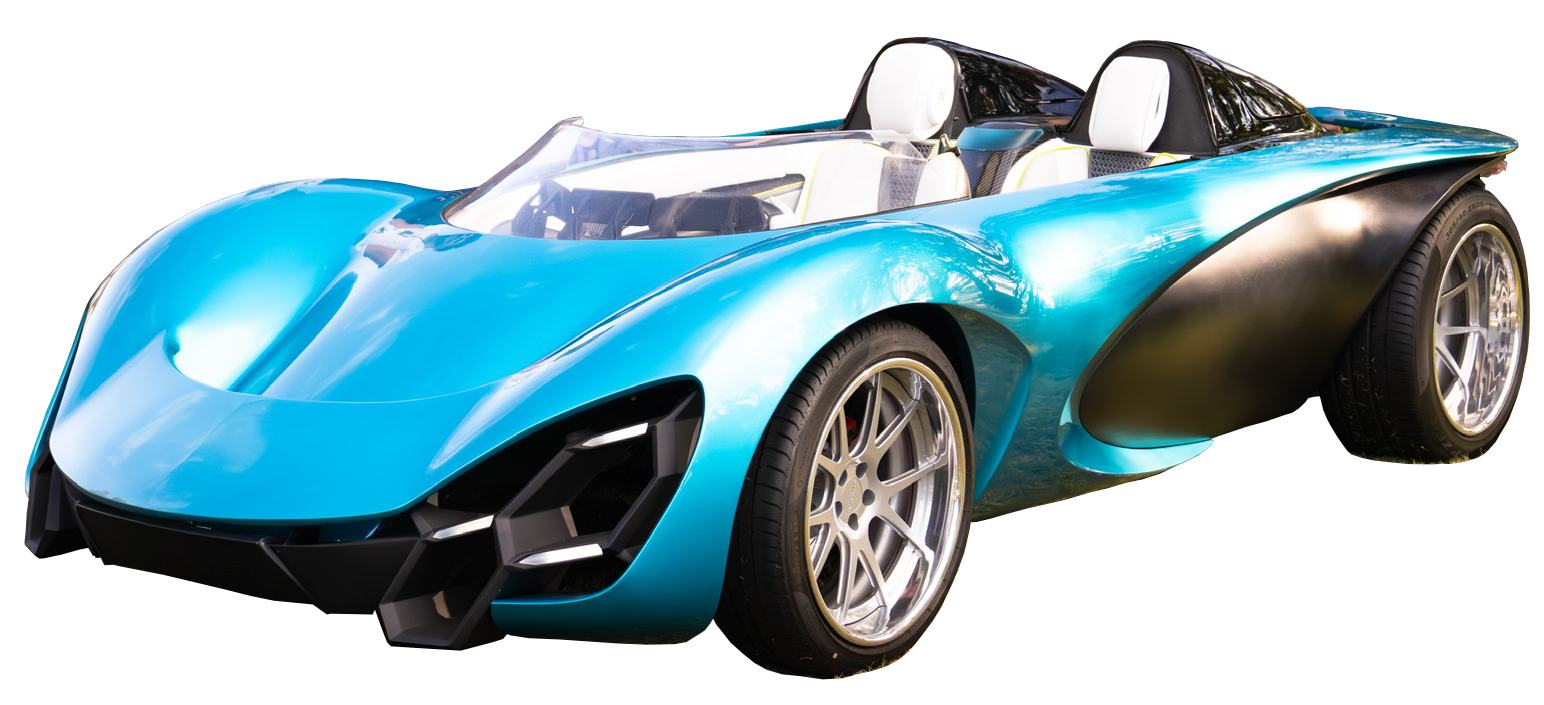
Aether was an unbelievable experience in creative problem solving, design language, engineering, manufacturing, CAD, and countless other skills. A team of designers including myself took this idea from rough sketches all the way through to a fully functioning car.
My biggest contributions to Aether were in bringing the concept to life. I helped to problem solve in manufacturing, strategize efficient production methods, lay out and assemble the interior, sand, lay carbon fiber, assist with mechanical work, and a do little upholstery.
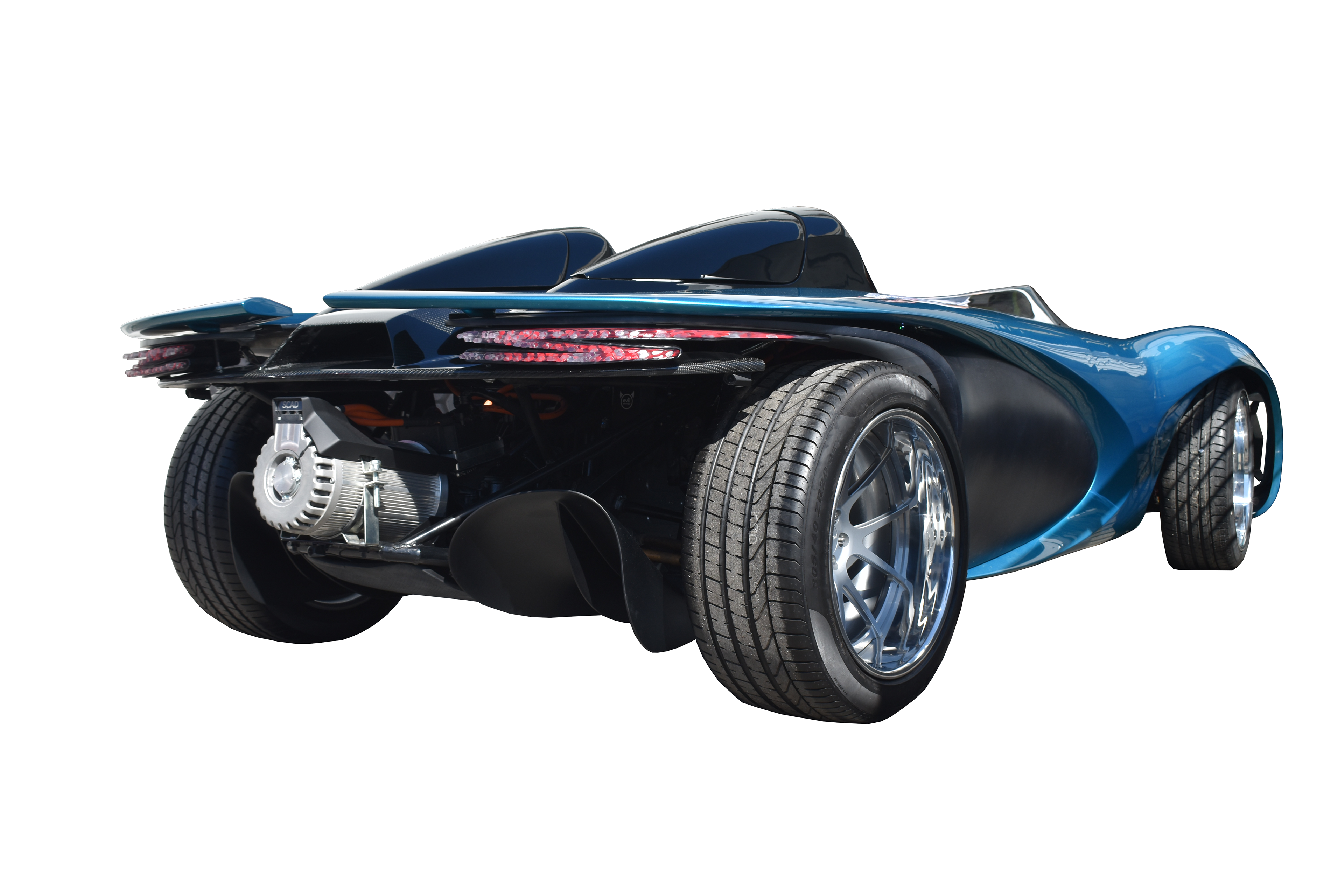
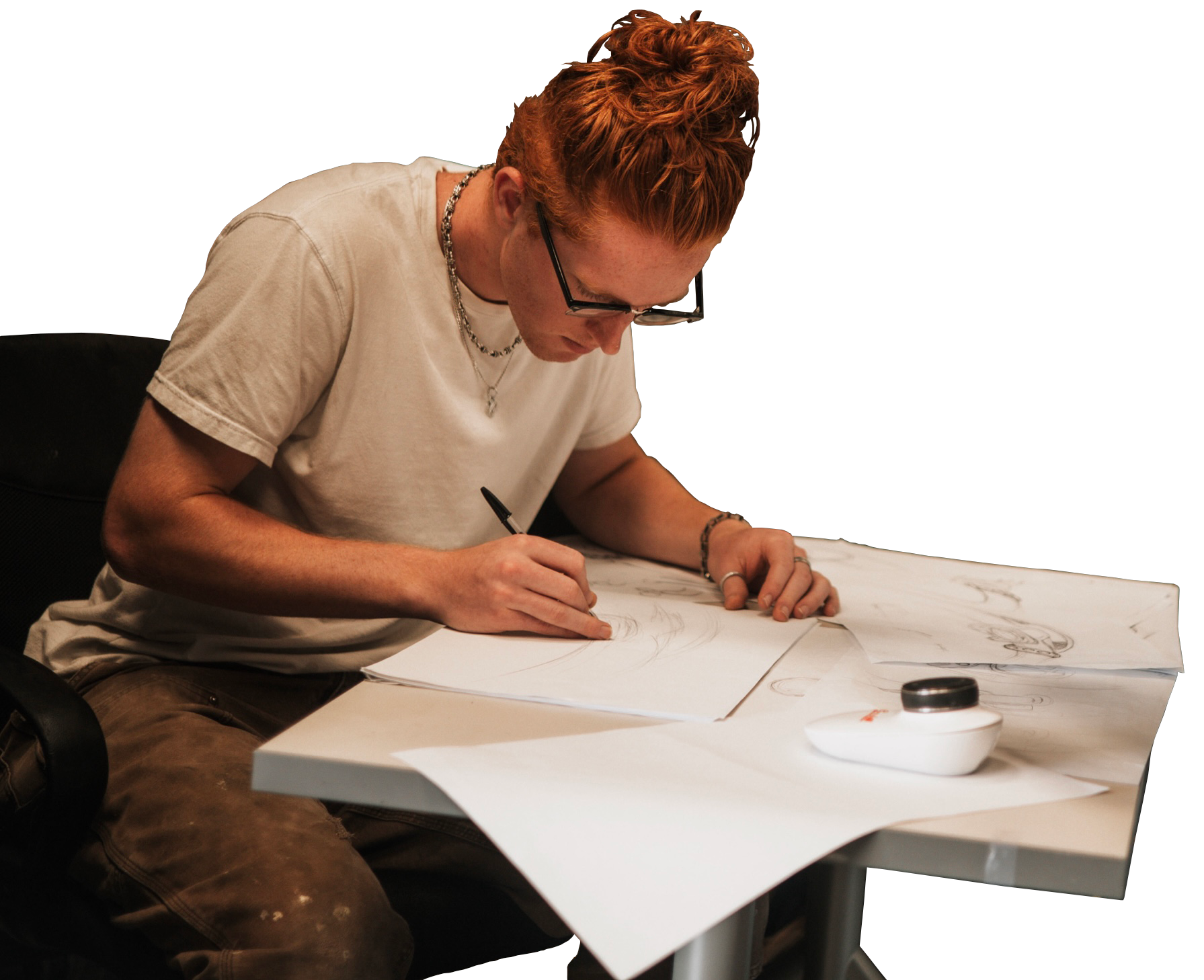
I also contributed directly to Aether's design. I helped ideate the car's exterior form early on, gave feedback on and produced proposals for elements in the interior, and designed the motor cover in the rear.
While still in the design phase, we needed a quick way to visualize the proportions of the car in real space. We created a laser-cut plywood grid structure from our CAD model, then filled the cavities with foam and hand-shaped it to Aether's contours.
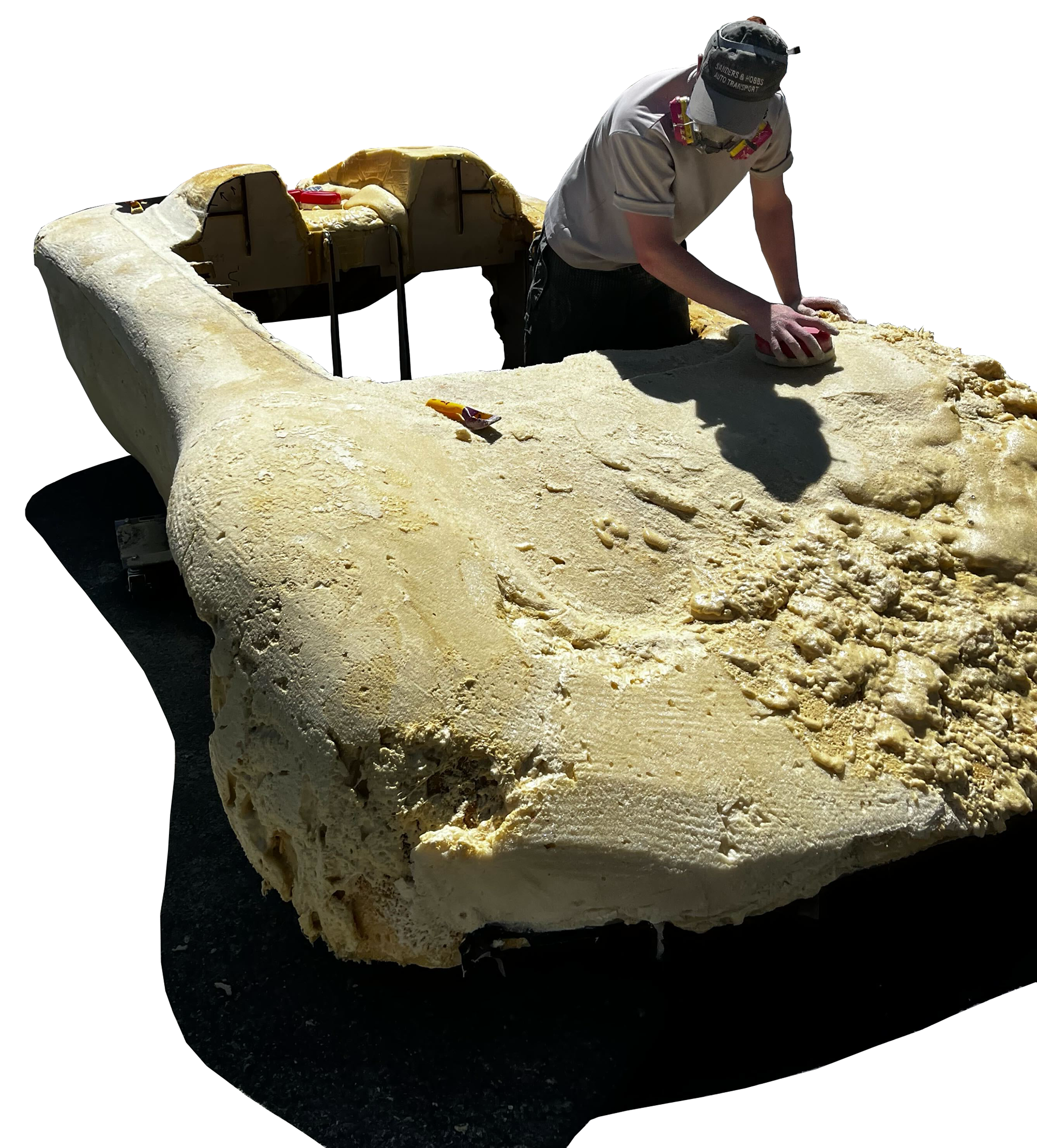
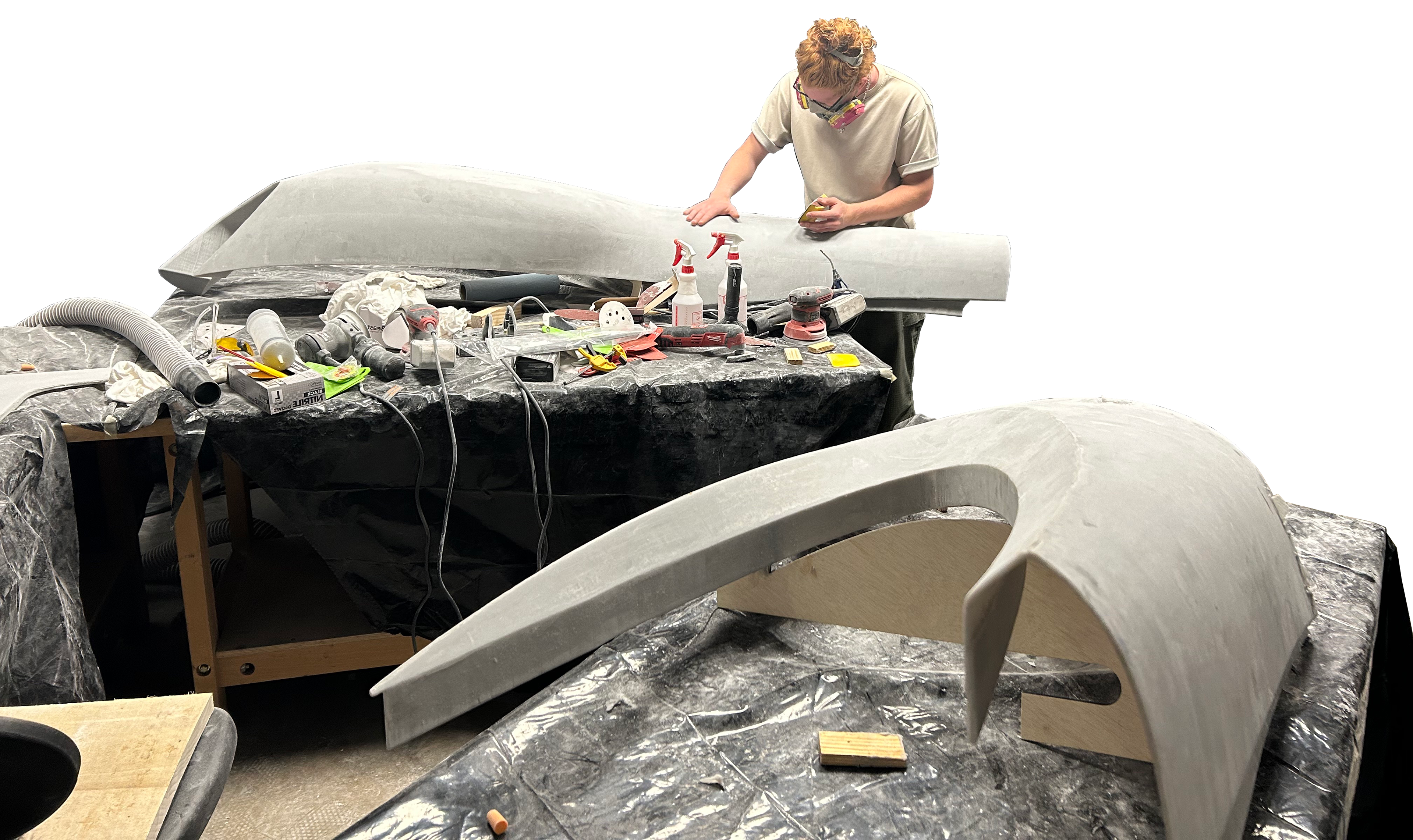
Aether is the first driving car to have its entire exterior 3D Printed. Because we were pioneering this manufacturing method, there were a lot of unexpected hurdles. There were also plenty of opportunities to get better at sanding.
One of the hurdles that arose from 3D printing was a lack of dimensional stability in the body panels. They perpetually warped and became misaligned. So, some of us on the project learned how to lay carbon fiber. We braced the body panels in their proper shape and reinforced the inside of each panel with a layer of carbon fiber. This kept the body light, but made it much stronger and more stable.
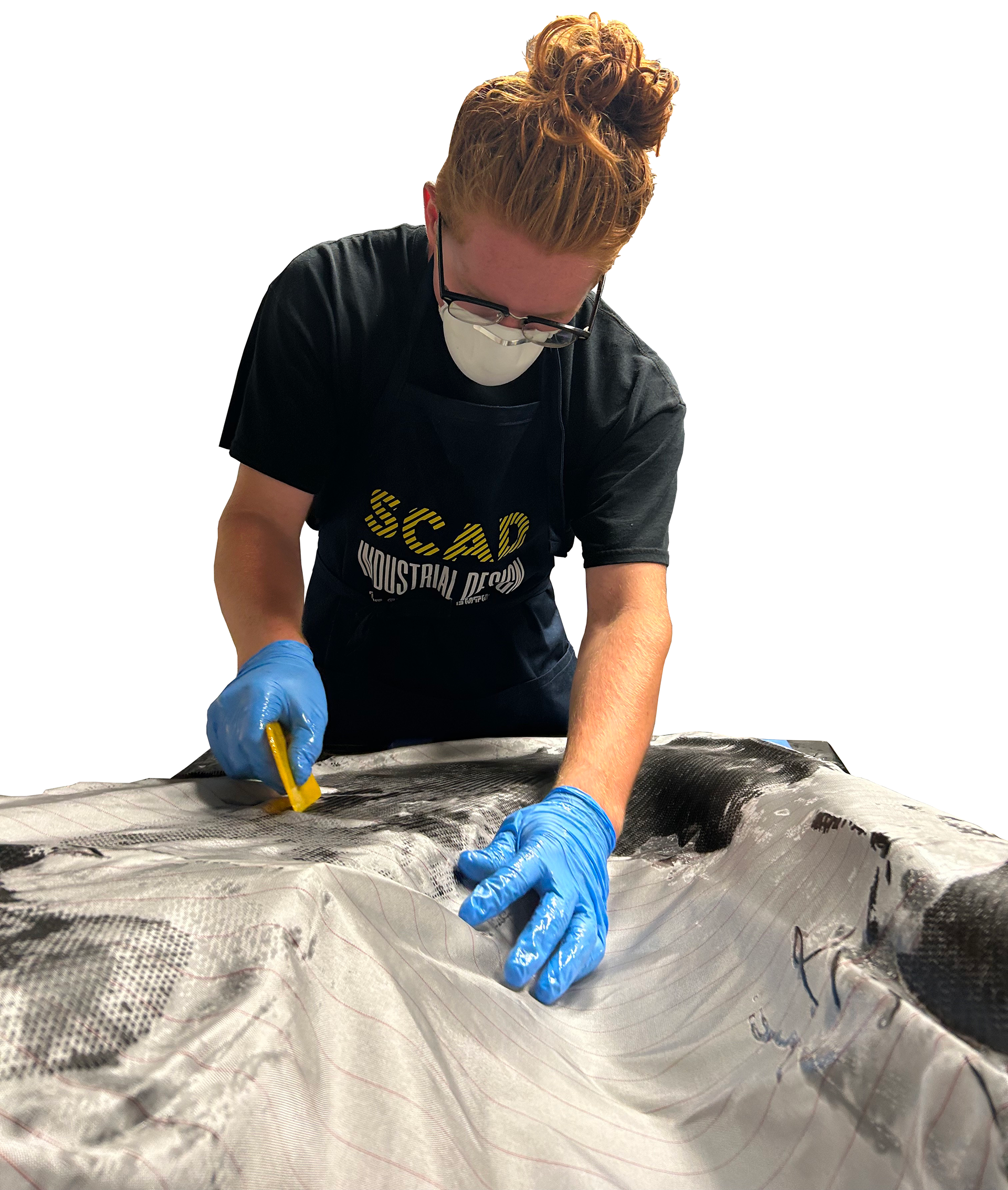
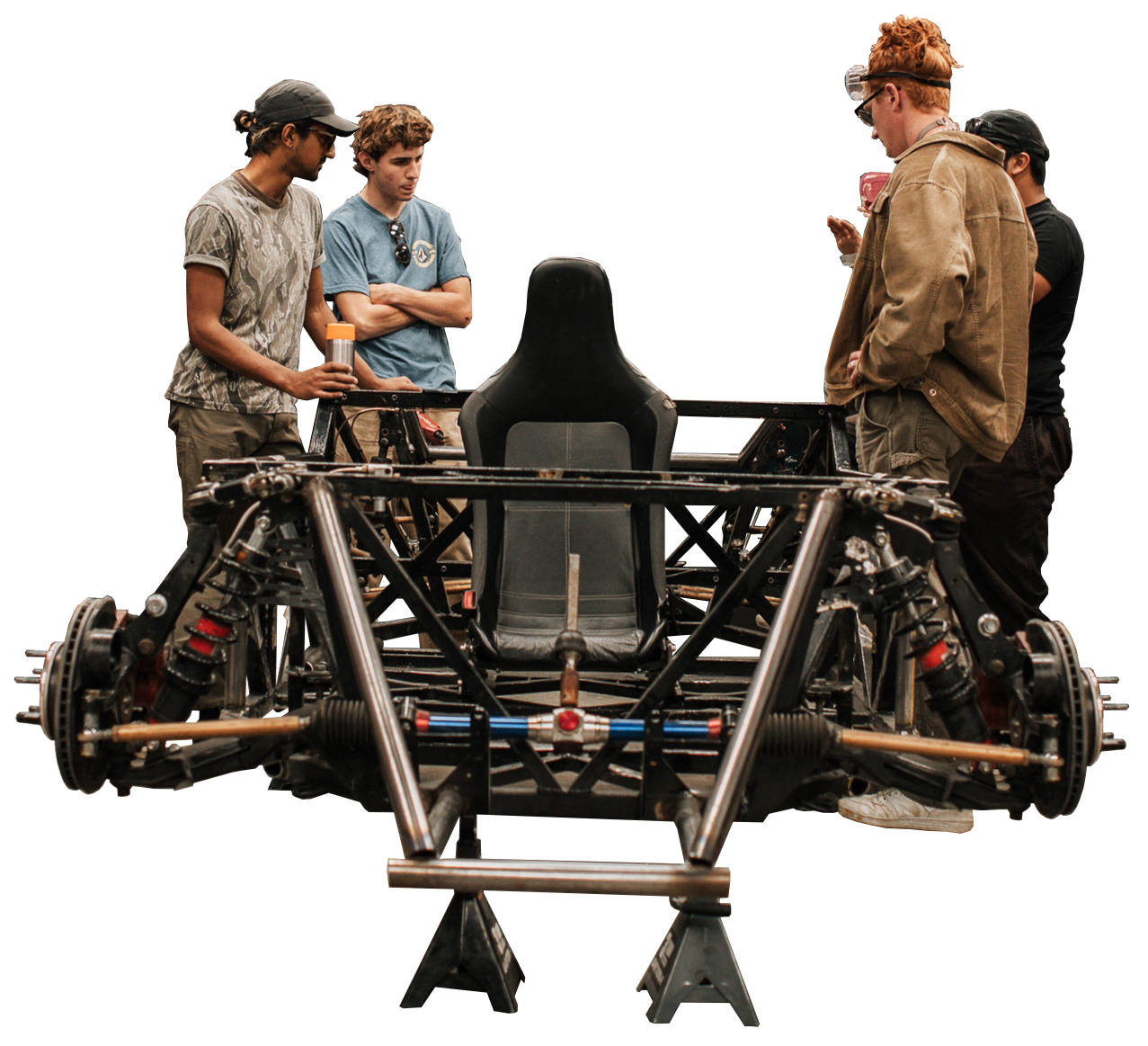
The elements beneath the body of Aether also required a lot of thought. We had to approach each problem with a design mindset geared towards things like serviceability and longevity, to ensure that Aether would be just as reliable as it is fun.